There’s two types of crushing
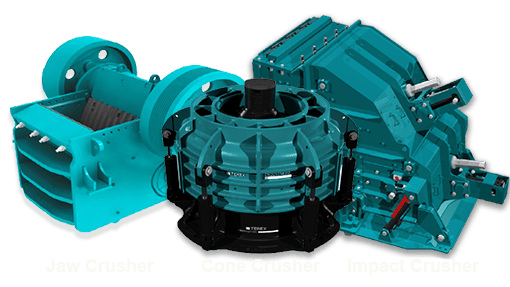
Compression & Impact Crushers
All crushers crush rock, but each one does it a bit differently. How they crush rock is what defines them and sets one apart from the other.
When you think about it, there are three ways to crush something.
- You can squeeze it so hard that it breaks. (Compression)
- You can throw it really hard at something so it breaks up when it hits. (Impact)
- You can hit it with something so hard, it breaks. (Impact)
Compression Crushers
Jaw and cone crushers use compression to squeeze rock between two surfaces until it shatters. These crushers generate an enormous amount of power and are able to crush a variety of materials including hard abrasive stone like granite.
Impact Crushers
Impact crushers rely on velocity and sudden impact inside the crusher to break the rock and stone. They provide a high reduction rate, but because of how they crush, they’re best suited for crushing soft to medium-hard materials like limestone.
How Crushers Work
Jaw Crushers
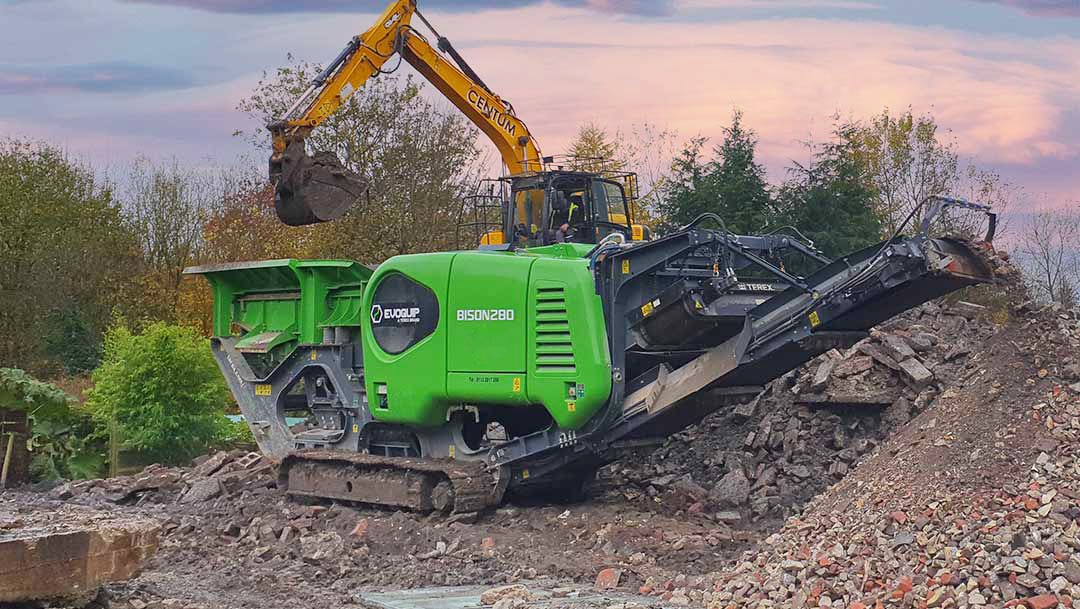
Mobile Jaw Crushing Plant
The crushing chamber of a jaw is a v-shaped cavity that consists of two jaws; one fixed and one movable. The movable jaw, also known as the swing jaw, is connected to an eccentric shaft that keeps the jaw continuously moving back and forth, opening and closing the jaw.
Rock enters the crusher through the feed opening at the top and is compressed between the two jaws. The chamber gets smaller as the rock moves through it until it’s been crushed small enough to fall through the opening at the bottom. This opening is the closed side setting (CSS), or the smallest size that can be crushed.
Learn more about our Jaw Crushers.
cone Crushers
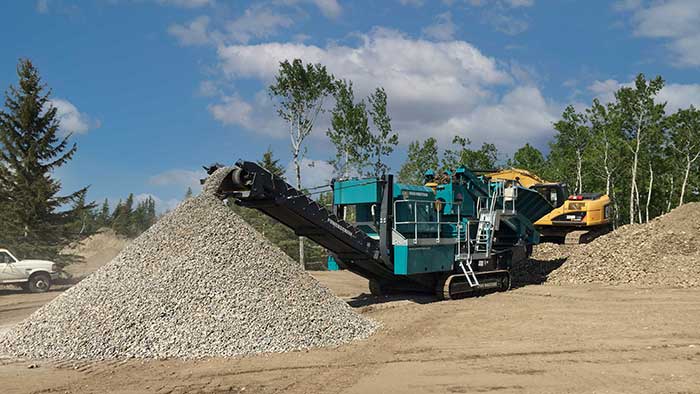
Mobile Cone Crushing Plant
Cone crushers are another type of compression crusher. They consist of a fixed concave and a mantle that gyrates in an eccentric motion.
The mantle is continuously moving and provides a constantly changing gap at the bottom of the crushing chamber. The smallest size of the gap is known as closed side setting (CSS) and represents the smallest size of material that can be crushed. The largest opening is the open side setting (OSS) and represents the largest size of material that can be crushed.
Material being crushed is caught between the mantle and concave, where it is compressed with enough force to fracture and break . The material stays inside the crushing chamber until it is crushed fine enough to fall through the gap at the bottom of the crusher.
Learn more about our Cone Crushers
impact Crushers

Mobile Impact Crushing Plant
There are two types of impact crusher, Horizontal and Vertical Shaft Impactors.
Horizontal shaft impactors (HSI) use the striking force of blow bars attached to a spinning rotor to fracture rock as it enters the crusher. They have a larger feed opening, accept larger feed size and have a high reduction rate which makes them ideally suited as primary crushers.
Vertical Shaft Impactors (VSI) are used in the secondary or tertiary crushing stages. They produce a consistent cubical-shaped finished product for road base, manufactured fines (MF), concrete, and asphalt material.
Learn more about our Impact Crushers
Configurations
Crushers are typically combined with other components like feeders, hoppers and conveyors and mounted on a frame or chassis. Depending on individual needs, plants can be stationary/modular, track-mounted mobile, or wheel portable.
Stationary and Modular Crushing Plants
Stationary plants typically reside in rock quarries and mine sites where they never move and stay for the plant’s entire life. They require a larger footprint and considerable infrastructure like buildings, walls, pads, and ramps to support the equipment.
Staionary equipment doesn’t move, which means that the feed source is continually moving further away from the crusher. This means longer loader cycling times, increased fuel consumption and wear and tear on equipment.
As the distance increases, material must be brought to the crusher by pushing it with a bulldozer, conveying, or hauling with trucks.
In contrast, wheeled and mobile plants can easily and quickly move from one location to another or maintain proximity to the feed source. Portability also makes it easier to replace one machine for another in the event of breakdowns or upgrades.
Mobile vs Portable
There are advantages and disadvantages to mobile and portable equipment. To some degree, equipment selection is based on application, but there are more practical considerations that may come into play.
Both tracked and wheeled chassis’ offer producers portability, versatility and flexibility. Portable setup times have improved over the years, but it still has to be spotted, set up, have cables laid out and connected to external power. Mobile equipment sets up in minutes, not hours.
Track-mounted mobile equipment has a smaller footprint and is completely self-contained. It doesn’t require external power, so it’s able to access remote locations and sites where space is limited.
Mobile Solutions Provider
Foreman Equipment specializes in mobile, track-mounted jaw, cone and impact crushers from Powerscreen and Evoquip.
We’ve been the Powerscreen Dealer for B.C. since 1984 and more recently, for Evoquip, the Compact Crushing and Screening Specialists. Our lineup of jaw, cone, and impact crushers from these two industry leaders covers everything from primary crushers with size and production capacities large enough for pit and quarry production to compact crushers small enough to fit into the most cramped job site.
Whatever you need to crush.
Whether you need to crush 200,000 tonnes in a pit or quarry, or 2,000 tonnes of concrete recycling on a C&D job, we’ve got you covered with reliable, cost-effective crushing equipment from Powerscreen and Evoquip.